What Does Effective FEA Look Like in 2021?
If you’ve been successfully doing FEA for years or decades, you have no doubt developed an effective process for getting the job done. But imagine you’re a smart, new innovator just starting out today — do you think you’re going to settle on that same old process, proven as it may be? The reality is:
- What once took a day now takes an hour.
- What once required human decision-making doesn’t anymore.
- What was once cost-prohibitive to use isn’t anymore.
These are paradigm shifts that advance the starting line for industry newcomers and have the potential to exponentially grow productivity, when in the right hands. The lesson is — effective FEA in 2021 makes total use of the technology of 2021.
What does it look like when you reconceive FEA for powerful distributed computing, for high-speed data and networks, for major process automation and streamlining? Let’s find out.
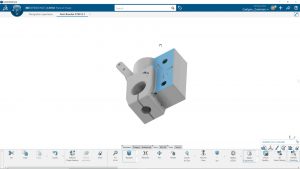
Adjusting a filleted face on an imported and
reparametrized STEP file in 3DEXPERIENCE
CAD Is Parametrized, Even When It’s Not.
Translated CAD is a headache many analysts are familiar with. It’s prone to missing, broken, or incorrect surfaces, and it cannot be easily modified. It can take a lot of time to correct broken CAD in order to turn it into FE. Worse yet, if we want to make any design modifications afterward, like changing a fillet radius, doing so purely on the mesh will be somewhat of a nightmare, if not impossible.
This doesn’t have to be the way to work anymore. In response to this common difficulty, the 3DEXPERIENCE Platform, built upon Abaqus and CATIA, has the Natural Shape app in it. Imported, featureless CAD can be reparametrized and then modified in a couple clicks. For a consulting analyst who doesn’t have access to his or her client’s design pipeline, this can be a major time saver.
Rules-Based Automeshing Does the Trick.
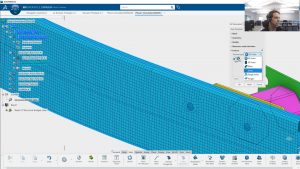
Marcel adds washer patterns to his bumper mesh
Many of us have become very accustomed to building mesh ourselves over hours and hours, making sure everything is just right. We’ve learned not to rely on automeshers or shortcuts, because they just haven’t done a great job and they miss the details. As a result, it could take days to create a suitable model, perhaps even weeks on a particularly large assembly.
There’s good news: rule-based automeshing has come a long way. 3DEXPERIENCE, for example, makes it easy to find features all over your CAD and apply modeling rules that ensure consistency and solution accuracy. These rules can be saved and applied wherever you want them, even other projects, letting one-time labor work for you again and again, a common trend in computing.
Assembly Connections and Contacts Take Minutes, Not Hours.
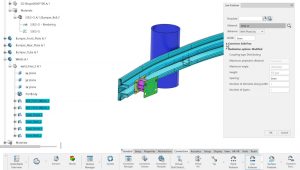
Creating the entire assembly’s welds
in FE by using the CAD data
One of the greatest pains of FE modeling is connections and contacts. Spiders on every hole, links on every node pair, contact faces on every touching surface? It’s a ton of work, it’s miserable, and, thankfully, it’s outdated. One again, a connected CAD-CAE pipeline means original design data can automate slow, tedious work like recognizing, defining, and meshing for bolts, welds, and even contact.
These are potentially day-long human-powered operations that can now be just another few seconds of automeshing calculation in 3DEXPERIENCE, regardless of how many bolts and weld lines you have. The Abaqus solver (and thus 3DEXPERIENCE) has also seen a lot of development in general contact. It’s now very robust and actually converges better than contact pairs, saving you the trouble of defining every interaction in your model, another well-known time sink for experienced analysts.
Material Assignments Are Automatic and Error-Proof.
Assigning materials in FE isn’t the most tedious of processes (unless your assembly is huge), but it does take time and it definitely introduces opportunity for error. What better way around this task than to use the material assignments already present in the CAD data? That’s another modeling task that we can leave in the past.
In 3DEXPERIENCE, a shared material database across the organization also means no more typing or transferring material cards with every project. Simply pick the material and the level of fidelity (nonlinearity, temperature dependency, etc.) from your library — no file transfer, no transcription errors, no redundant work.
Analysts Can Tweak or Update the Design and Rerun Almost Instantaneously.
We’ve all looked at our FEA results and seen an obvious change that would improve them. What’s the next step to verify that?
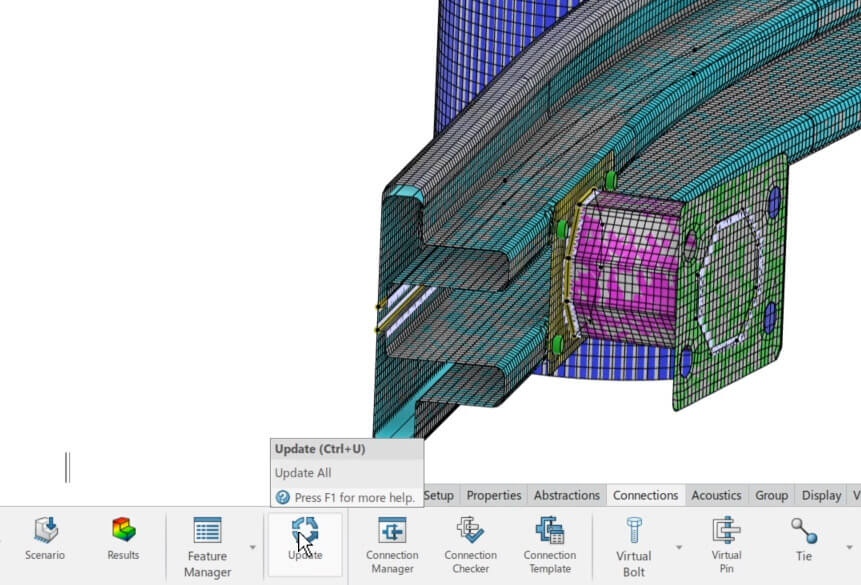
One button to update the full, connected assembly FE.
There’s the old way:
- Write an email to the designer
- Wait for him to update the CAD
- Download the CAD
- Import it into your model
- Cut out the old FE
- Remesh the changes
- Attach the new FE
- Export the deck
- Run the solver again
And there’s the new way:
- Type in the new parameter values yourself
- Click “update FE model”
- Launch the simulation again
I’d rather do the new way. This kind of workflow is enabled by the unbroken chain of data from CAD to CAE and back, as provided by solutions like 3DEXPERIENCE.
Rules and Templates Have Reduced or Eliminated Much of the Iterative Analysis Workflow While Also Improving Consistency.
A comprehensive iterative update to your model may include substantial changes to nearly everything in the assembly. While the fundamentals remain the same, in the traditional way of FE modeling, that could still amount to basically doing everything over again. This is where rule-based modeling really shows its strengths, especially with recent improvements to automeshing algorithms.
Rather than exercising your modeling judgment on every meshed surface in the model again, if you can instead just apply a template, or set of modeling rules, to each component and let the computer do the rest, you can churn out iterative analysis in a fraction of the time it used to take. Modeling templates can also grow to encompass model interactions, analysis outputs, and more. These rules and templates are, essentially, inviolable modeling guidelines that can also ensure consistency across different iterations, projects, and even analysts.
The best way to manage both the project data and the processes is within a single platform like 3DEXPERIENCE. That way, those templates are just a few clicks away.
Freely-Accessed File Systems Are No Longer the Best Way to Manage Your Data.
Who likes to go through their files, do FTP transfers, and deal with hard drive failures? No one! The best place for your files to reside is on reliable enterprise storage, whether on-premise or on-cloud, within a shared project structure that you don’t have to personally manage. This is the direction things are going for a reason:
- You’re protected from catastrophic data loss.
- You don’t have to organize and synchronize your own file system.
- You don’t have to manually send, receive, and archive files.
- You’re able to quickly access your work from any computer with a network connection.
You get all that with platform solutions like 3DEXPERIENCE.
You Don’t Model Up Several Design Alternatives — You Propagate an Optimization Study from One Design.
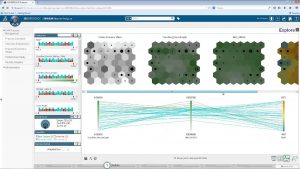
Comparing simulation results from 50 autogenerated,
multivariable design options
Does your designer hand you several options for a part and you have to pick the best? What about all the rest of the possibilities? The best answers aren’t always obvious, especially with multiple competing factors to consider. That’s where optimization processes can both reduce the labor of the analyst and improve the results by automatically generating and testing more possibilities. By using the appropriate CAD and CAE tools to define the model, you can prepare it to automatically converge on the best designs.
As CAE platforms grow and mature and unify, this kind of workflow is becoming more accessible to more design stakeholders (available in 3DEXPERIENCE as Process Builder and Generative Design, using Isight and Tosca technology under the hood).
Large Models and Results Files Are Not the Difficulty They Used to Be.
What’s a big file now? 2GB? 8GB? 40GB? 120GB? As processing power explodes, so does data storage capacity and transfer rates. All that together means larger and more complex simulations that may push the limits of both hardware and software not prepared for such progress.
In other words, legacy software packages may not be efficient for today’s larger file sizes, and the differences could be dramatic. This could manifest in, for example, essentially impossible animation tasks in the post-processing phase.
You may find that newer applications are better built from the ground up to handle data on a different scale. Of course, to get to that point, you need the computing power for huge simulations in the first place…
Anyone Can Afford Enterprise-Level Computing Performance.
Computing hardware can cost a ton, and that’s just the start. You also have to invest time and energy into so much:
- You need to research and buy the right stuff (watch out — you can make some spectacularly wrong choices!)
- You need a specially-built place to put it.
- It costs to run and to cool it.
- You need trained staff to maintain it.
- It may require additional software licensing to use.
There are certainly situations where the benefits outweigh the costs, but this list is, in general, why all industries are moving toward cloud solutions. When someone else centralizes and manages that stack of responsibilities and costs, that saves you a boatload of money and time.
But… it also eliminates barriers to entry and raises the floor of CAE quality (and thus engineering output!). If an agile, hungry startup is operating on enterprise resources, that’s a real predator with unprecedented disruptive potential. The good thing is that, almost by definition, getting into cloud FEA like Abaqus Power’By or 3DEXPERIENCE is as easy as signing up!
Why It’s Time to Reassess Our FEA
The last several years have brought about seismic shifts in the way we do digital business, and these changes cannot be ignored. FEA today isn’t the FEA of yesterday “but faster”:
- FEA today is an open, two-way connection with design data and personnel.
- FEA today has eliminated many of the most tedious and time-consuming aspects of FE modeling.
- FEA today has restructured its model preparation labor to be highly reusable and scalable.
- FEA today can exhaustively optimize engineering output with automated processes.
- FEA today reduces or eliminates costly IT distractions regarding data and computing.
- FEA today is, yes, faster — and also higher fidelity.
- FEA today brings enterprise computing to everyone everywhere with cost-effective cloud solutions.
The latest engineering simulation tools address longstanding user frustrations and time sinks by finding completely new ways to handle many things we used to take great pains to do manually. Even from the very first step of importing CAD, there are foundational new approaches that can bring tremendous benefits to the process. These benefits roll over into many of the most tedious and time-consuming analysis tasks, into collaborative workflows and their associated labor, and even into some of the real decision making to solve complicated engineering problems. And, due to evolving cloud business models, all of this technology is more accessible than it’s ever been, so that one engineer can operate with the resources of an industry juggernaut.
The sharpest minds can nurture good ideas as fast as they can think them up, no longer subject to the leveling effects of slow and/or expensive computing. It’s an exciting and crucial time to reassess your FEA process if you haven’t done it in a while. So much has improved in not just the speed of the solvers, but how we actually make models and collaborate with our team, and who can access this fantastic technology. It really unleashes us to do more of what we love to do — the actual engineering!