SOLIDWORKS Electrical: Adopting a Library System
Did SOLIDWORKS Electrical come with library content that you may never use? Are you having trouble distinguishing between company parts and other non-company parts? Are some of your used parts not quite completed in SOLIDWORKS Electrical while others are? Are you tired of having to always filter for your company created content? If you have answered yes to any of the above questions, then this blog is for you.

SOLIDWORKS Electrical allows you to create your own libraries for organizational purposes for your manufacture parts, symbols, title blocks, cable references, and macros. This can be done in the Library tab ->Libraries Manager.
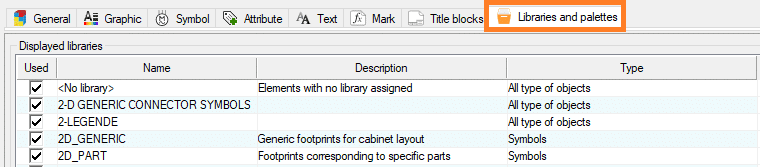
In the configuration settings, you can also specify what libraries that project automatically filters for. This is best incorporated in a template and allows you to divide out all your company’s parts and content while also keeping other content ready for use should the need arise. As a best practice, you can even create a two-library system for company content that is in-work or approved.
The only shortcoming with a company library system is how do we confirm if all are components used in a project come from a company organized library? There are two ways to efficiently do this, and I recommend incorporating both methods.

First, you can have the PDM connector installed. This allows you to synchronize specific libraries to PDM. Upon checking a project in you will get a warning instructing you which parts in your project are not in your synchronized library, so if we synchronize just the company libraries with PDM we have effectively created a check for when we use content outside of our library system.

The second method is creating a design rule check that provides feedback on parts that are not in your company libraries. The design rule check can be consulted regularly and does not require a PDM check-in to verify.
We have determined how a company library or library approval system can be advantageous. Now the question is how we effectively move our used components from their various libraries into our newly created library system. In our various SOLIDWORKS Electrical managers, we can filter for and multi-select several items and then change the libraries all at once by through the property’s icon. The problem with this is how do we filter for all are company content to begin with? To identify company content, we could export to excel a report containing the manufacturer and manufacturer part number for each existing project. Then a column can be added to these documents containing the libraries you would like to move the parts to.
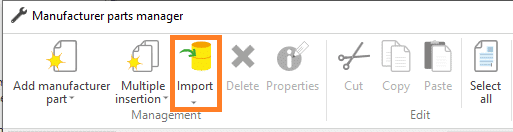
This new excel document can then be imported effectively moving all old project parts into their desired libraries.
You now have the ability to organize pre-existing project content into a company library system that can even incorporate an approval process for validating and completely documenting a part. Newly created projects can then be verified that they are indeed using company scrubbed content through a design rule check and/or check in to PDM. This helps us build trust in the integrity of our database content and allows us to utilize the automation and standardization features more effectively in SOLIDWORKS Electrical.
Mark Talbott
Sr. Application Engineer Specialist, Electrical
Computer Aided Technology, Inc.